United Arab Emirates+Vacuum Drum Filter+Acrylic Fiber Factory
Product: Vacuum Drum Filter
Country: United Arab Emirates
Application: Acrylic Fiber Factory
Vacuum drum filter is a kind of continuous filter. The construction is similar to that of a rotary drum vacuum filter, and the principle of operation is the same. It is a continuous filter with negative pressure as the filtration driving force and the filtration surface is on the surface of the cylindrical drum. Originally used in the alkali and mining industries, this filter was later extended to sectors such as chemical, coal and sludge dewatering. Widely used in food, medicine, organic chemistry, wastewater treatment, oil and other industrial sectors.
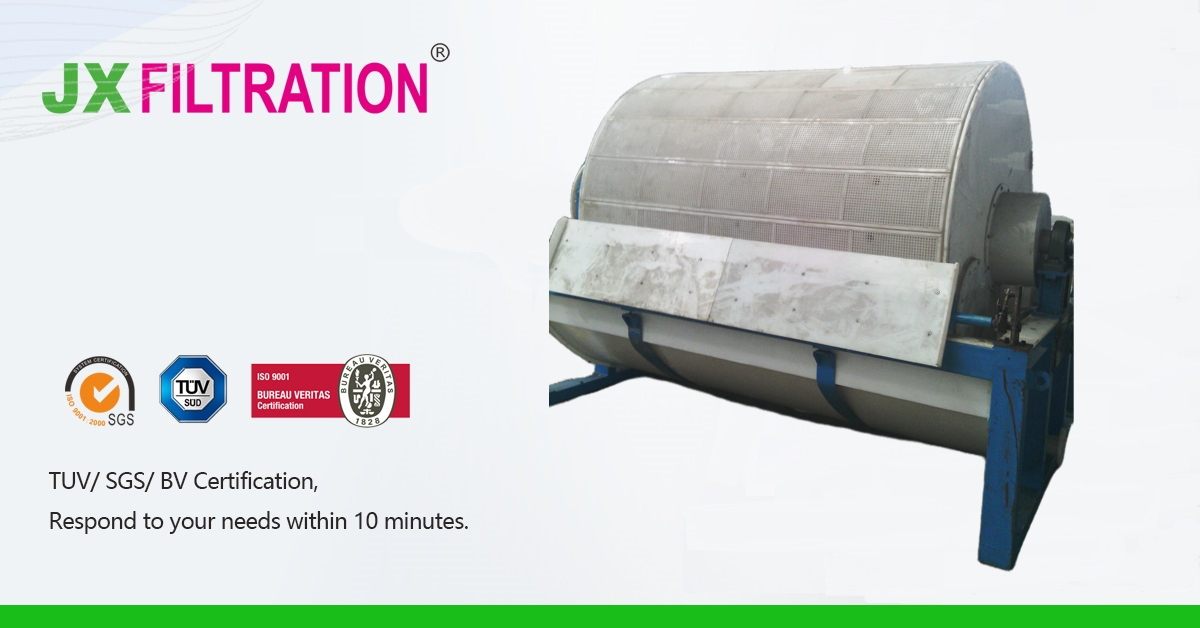
- Type: Vacuum Drum Filter
- Material: SS 304 /316 L
- Power: 0.75kw
- Productivity: 65-340m³/h
- Warranty time: 1 year
- Capacity: 65-340m³/h
- Weight (KG): 700 kg
Influencing factors of filtration effect of vacuum drum filter:
1. There are many oily and suspended solid impurities in the feed of the vacuum drum filter, which can block the pre-coating surface of the drum in a short time, increase the filtration resistance, and reduce the filtration speed of the feed liquid. In this case, in order to maintain the processing capacity of the filter, while ensuring the normal operation of the drum stirring, the only way to continuously remove the contaminated surface layer of the diatomite pre-coating is to increase the frequency of knife feeding and reduce the filtration resistance of the feed liquid, which greatly increases the consumption of diatomite.
2.The effect of drum cleaning:
The so-called drum cleaning refers to washing the surface of the drum and the accumulated diatomaceous earth in the cavity after removing the vacuum. The cleaning effect of the drum is not good. Because the residual diatomite etc. block the flow channel or increase the resistance of the pre-coating process, the thickness of the diatomite pre-coating is uneven, and "collapse pits" or "deep grooves" appear, which affects filtration effect.
3. Influence of vacuum degree during drum precoating
The drum pre-coating process is based on the vacuum as the driving force and the circulation of the material keeps the diatomite on the filter cloth on the surface of the drum to form a pre-coating with a certain thickness. When the drum is pre-coated, the vacuum degree should not be too high. When the vacuum is too high, the pre-coat layer formed is relatively dense, the filtration resistance of the material and liquid increases, and the filtration effect becomes poor.
4. Influence of pre-coating liquid:
When preparing the pre-coating solution, the amount of diatomaceous earth and water should be appropriate. Excessive addition of diatomite will make the pre-coating too thick, increase the filtration resistance, lead to the rapid consumption of the pre-coating at the initial stage of use, and increase the filtration resistance. The consumption of diatomite is added; the addition of diatomite is too small, the pre-coating formed is thinner, and the service cycle of the drum pre-coating is short, which increases the frequency of pre-coating and the amount of labor; The diatomite in the precoating solution is too concentrated, the formation time of the diatomite coating during the precoating process is short, the distribution is uneven, and the filtration effect is not good.
5. Influence of Diatomite Particle Size
Diatomite has a uniform particle size, and the filtration resistance of the pre-coating and filtration is equivalent, which is conducive to the formation of a uniform drum pre-coating, and the filtration effect is better.
After-Sale Services
- Quality guarantee: 12 months after the equipment having been operated.
- Satisfied after-sell service: free maintenance and inspection.
- Detailed installation instructions, CAD drawing and product qualification certificate.
Any Requirements, Contact Us Now!
Nina
Email/Teams:nina@filtrationchina.com
Mobile/Whatsapp/Wechat: +86 17269571060
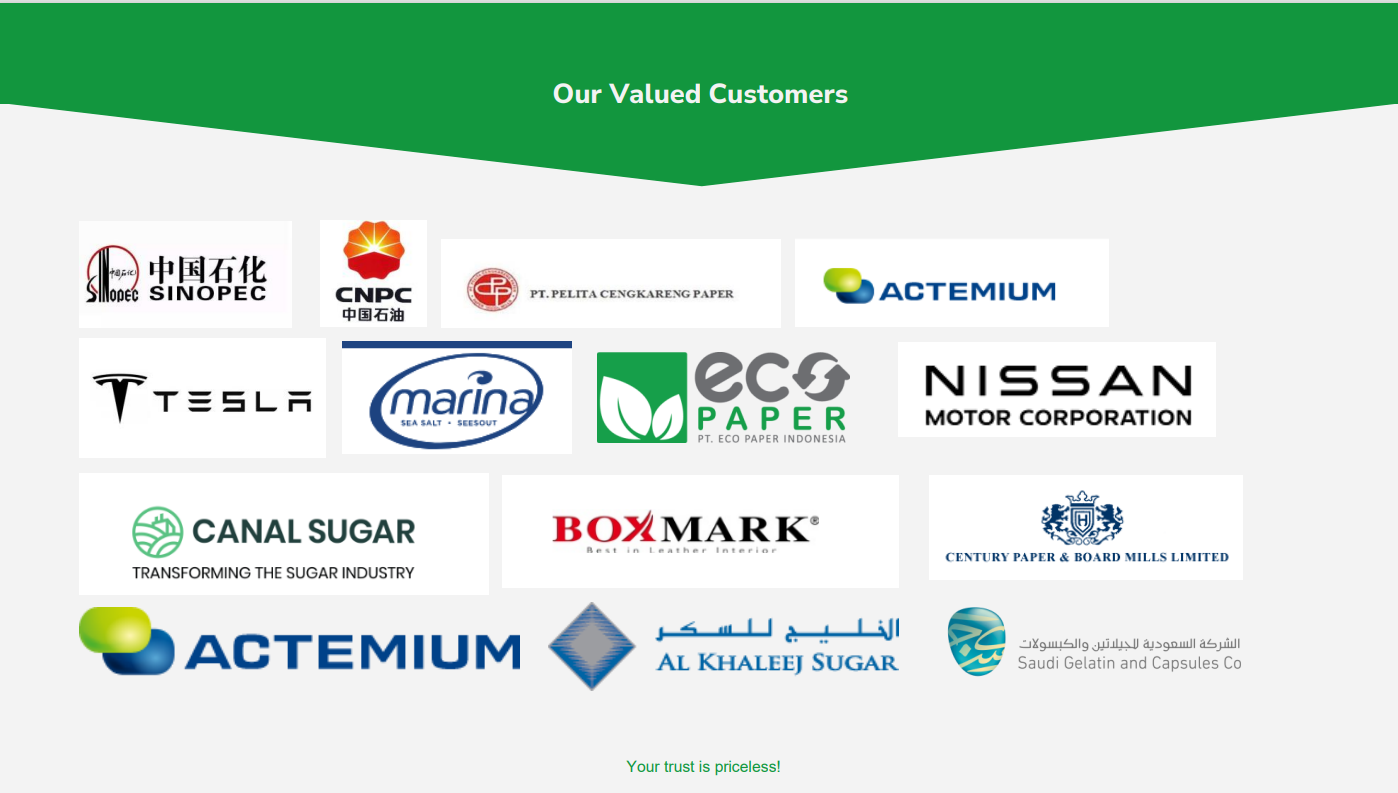