Technical Essential of Horizontal Centrifuge
- Lower investment in infrastructure construction and better on-site operating environment
Compared with traditional filtration equipment (plate, frame, belt, etc.), the high-performance centrifuge has a compact structure, high efficiency, and covers an area of about 1/3. No need to be equipped with auxiliary air sources, high-pressure water, etc. The outlet pipeline structure is simpler, and entire equipment is fully enclosed to operate and convenient to install and move. It is widely used in the harmless treatment of oily sludge from oil field drilling. - Stable operation, low failure rate, low maintenance cost
Compared with filtering equipment, the centrifuge does not need any filter cloth or filter screen, so there is no trouble of clogging and no need to replace the filter cloth. - Modular design: easy to learn and operate the equipment
Design concept: reduce the skills, cultural level requirements and labor intensity of equipment operators. The control system can realize one-click start and stop, fault self-diagnosis and safety self-protection. - Operator configuration and labor intensity
The high-performance centrifuge is an automatic and continuous operation equipment that realizes the separation and discharge of the feed (liquid). The whole process does not require human intervention. No need manual discharge. - Ingenious, unique and diversified heavy liquid phase discharge structure
The heavy liquid phase separated by the three-phase centrifuge can adopt two different liquid methods: gravity discharge and centripetal pump pressure discharge. The centripetal pump pressure discharge includes liquid layer fixed mode and the online adjustable mode , which can be selected according to the requirements of the process conditions. - High-performance, wear-resistant and corrosion-resistant hard alloy
Because the oily dirt contains a lot of small hard particles and impurities such as sand, glass, metal, etc. Based on the characteristics of the material (PH, corrosive material, solid particle size and hardness, etc.), we suggest to adopt hard alloy (YG6,YG8) or porcelain, the hardness can reach 89-93 (HRA). - High-performance stainless steel material
The high-performance three-phase centrifuge is equipped to recover 90% or more of 95% of the oil, and adapt to the liquid density difference (oil and water comparison) and gas oil of different densities (0.1-0.08g/cm), which is required the separation factor above 3000G can achieve a more ideal separation effect. To ensure the stability and service life of the centrifuge, high-strength duplex stainless steel SAF2205 with better corrosion resistance is used. - High dryness screw conveyor and drum structure
The dehydration of solid particles mainly relies on strong centrifugal force, high-torque screw extrusion force and ultra-long solid particle dehydration length. The centrifuge can produce centrifugal force more than 3000G which is 30-50% higher than the ordinary centrifuge, the drum dehydration length is 10-20% longer than the ordinary centrifuge.
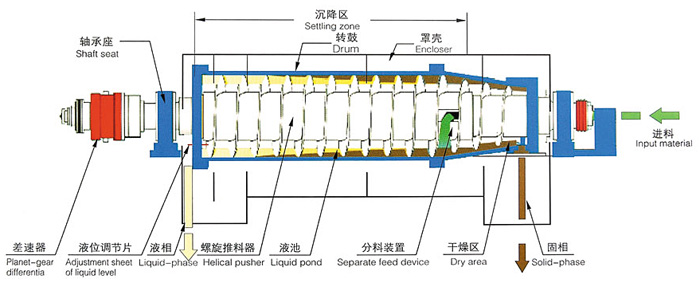
- High torque involute planetary gear differential
Ultra-high pushing torque requires a high-torque involute planetary gear differential as the basis. The differential equipped with the centrifuge has the characteristics of high torque, high rotation, low heat generation, and excellent thermal performance to ensure that the centrifuge can run stably for a long time. - CIP cleaning system
The fully automatic control system is equipped with a CIP cleaning system, which can effectively solve the problems of inadequate cleaning and incomplete cleaning during the shutdown process, and can effectively avoid equipment problems caused by human factors. - Humanized configuration of centrifuge
Spiral bearing (located in the drum, relatively concealed) lubrication technology: complete the filling of lubricating oil outside the hood. The hood adopts a hinged opening structure and is equipped with high-pressure strut assisted opening
Vibration and temperature sensor at the main bearing seat (optional) - Centrifuge light-phase liquid layer adjustment technology
JX centrifuge adopts the advanced technology: after opening the hood, user can easily complete the adjustment of the light phase liquid layer. - Variable pitch technology
Using this technology can effectively reduce the screw pushing torque, improve the processing capacity, and further reduce the moisture content of the sediment. - High rigidity spiral rotor technology
The rigidity of the spiral rotor directly affects the stability and safety of the equipment. Through theoretical analysis and calculation, the working speed of the high-rigidity spiral rotor is far away from the first and second critical speeds which can avoid the resonance state at high speed. - Double motors, double frequency conversion common DC technology
The main and auxiliary motors of the centrifuge are each controlled by a high-performance VFD. The auxiliary motor is always in the generator state under the action of the differential speed. Due to the common DC technology of the inverter, the auxiliary inverter can convey the energy generated by the auxiliary motor for main motor, so as to achieve the purpose of energy saving and consumption reduction. This technology can realize the stepless adjustment of the centrifuge differential speed, and has the advantages of fast reaction speed, accurate torque detection, stable torque control, and low failure rate. - Constant torque control technology
Real-time monitoring of the actual output torque of the constant-torque variable frequency motor through the high-performance auxiliary inverter, and comparison with the set torque value. Real-time adjustment of the screw conveyor pushing speed through PID, the centrifuge can achieve continuous, stable and economical operation.
Any requirements, contact us now!
Grace
Email:grace@filtrationchina.com
Mobile/Whatsapp/WeChat:+86 17269571160
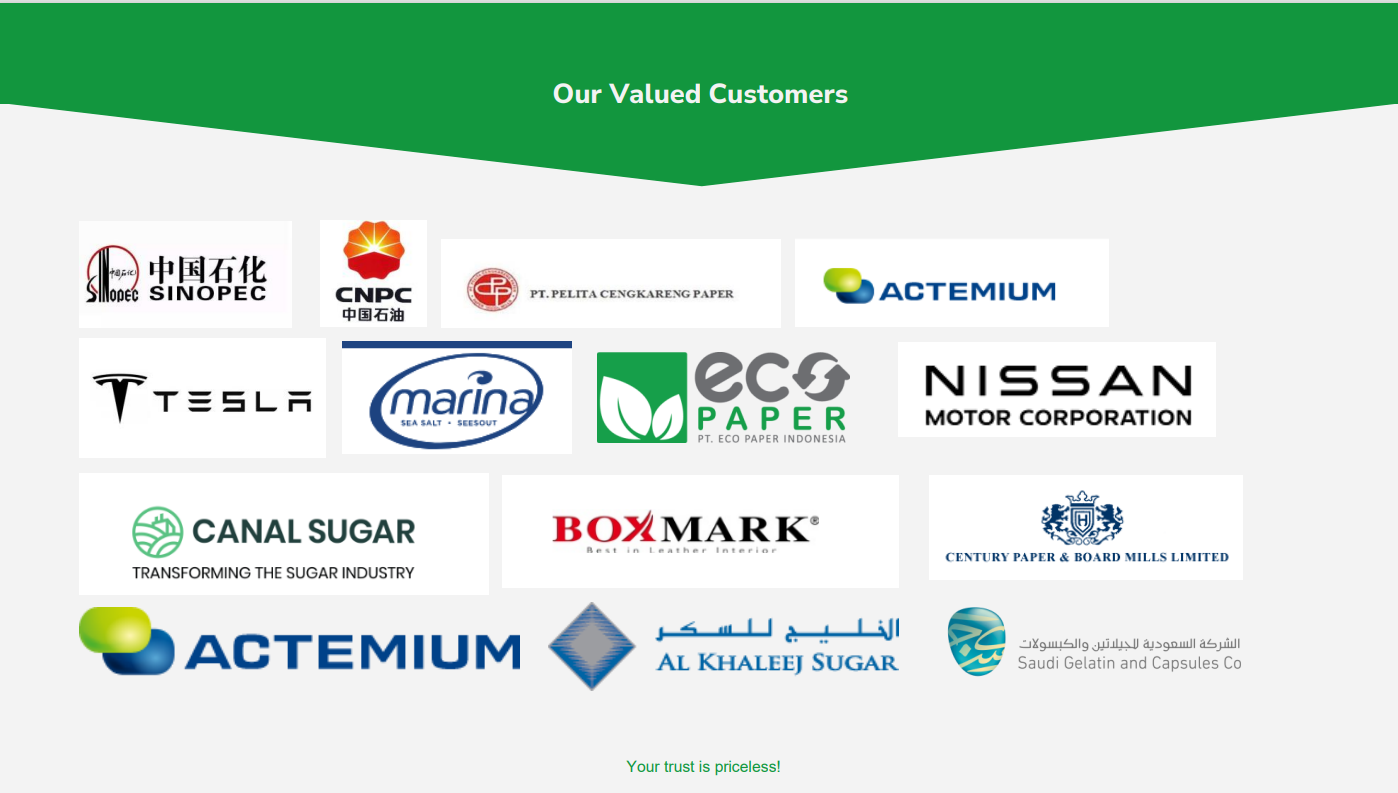