Why Choose a Vibrating Screen?
Vibrating screens are widely used in industrial production due to their high efficiency, excellent adaptability, and operational convenience. Below are the key reasons for selecting vibrating screens and their typical applications:
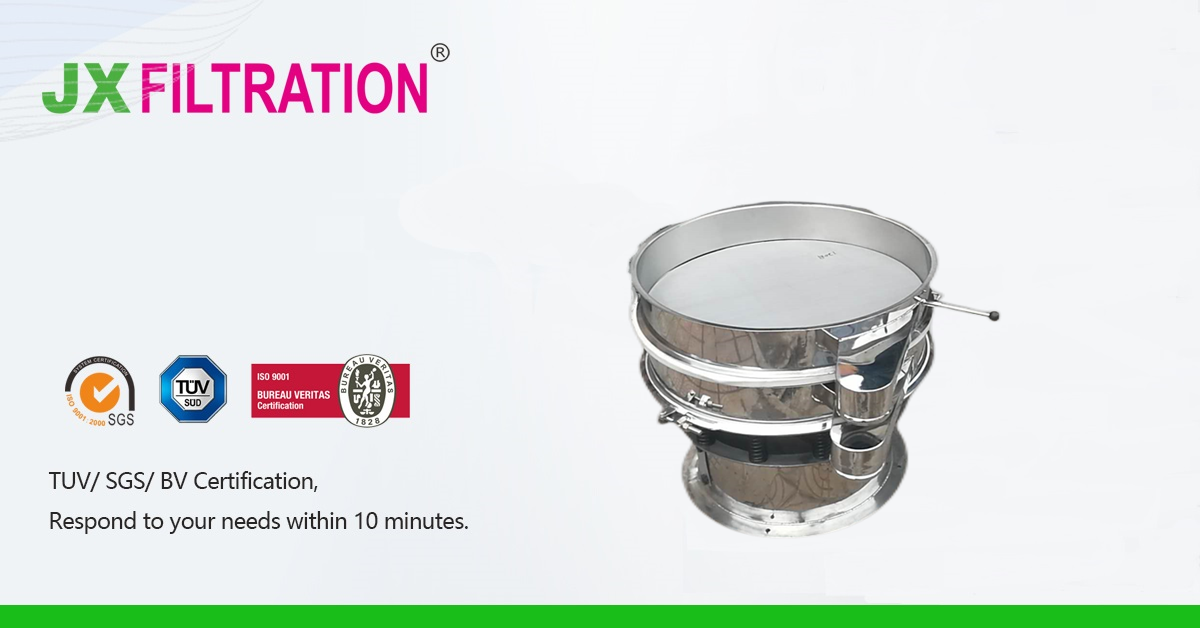
- High-Efficiency Screening with Large Capacity
- Rapid Separation: The vibrating screen generates high-frequency vibrations through an electric exciter or vibration motor, causing materials to be quickly tossed and dispersed on the screen surface, significantly improving screening efficiency (5–10 times faster than static screens).
- Multi-Layer Classification: Can be configured with multiple screen decks (typically 2–5 layers) to separate multiple particle sizes in a single pass (e.g., coarse, medium, and fine particles in ore screening).
- Continuous Operation: Suitable for large-scale industrial production, such as continuous screening in grain processing or mining crushing lines.
- Adaptability to Complex Materials
- Dry and Wet Screening Capabilities:
- Dry Screening: Handles powders and granules (e.g., fertilizers, quartz sand).
- Wet Screening: Processes slurries and suspensions (e.g., mineral slurry, mud), with spray systems to prevent clogging.
- Sticky or Clog-Prone Materials:
- Ultrasonic vibrating screens can handle high-viscosity materials (e.g., herbal extracts) by using high-frequency micro-vibrations to prevent screen blockage.
- High-Temperature or Corrosive Materials:
- Materials like stainless steel, polyurethane, or Teflon coatings can be selected for resistance to heat and chemicals (e.g., catalyst screening in the chemical industry).
- Precise Grading and Quality Control
- Controllable Aperture Size: Screen mesh sizes range from micrometers (e.g., 20μm pharmaceutical powders) to tens of millimeters (e.g., crushed stone), meeting various precision requirements.
- Reduced Over-Grinding: The gentle tossing motion minimizes breakage of brittle materials (e.g., grains, pharmaceuticals).
- Impurity Removal: Used in the food industry to eliminate foreign matter (e.g., metal scraps, insect eggs).
- Low Maintenance and Long Service Life
- Simple Structure: No complex transmission parts, resulting in low failure rates (e.g., linear vibrating screens only require periodic motor checks).
- Self-Cleaning Design: Bouncing balls or ultrasonic devices automatically clean the screen, reducing downtime.
- Modular Replacement: Quick-release screen mesh design for easy maintenance.
- Cost-Effectiveness
- Low Energy Consumption: Compared to centrifugal or air-flow screens, vibrating screens require less power (e.g., standard rotary vibrating screens use only 0.5–3 kW motors).
- Versatility: Different materials can be processed by simply changing the screen mesh, reducing equipment costs.
- Wide Industry Applications
- Mining: Ore classification, tailings dewatering.
- Chemical Industry: Plastic pellets, resin screening.
- Food Industry: Flour, sugar, spice filtration.
- Pharmaceuticals: Quality control of powders and granules.
- Environmental Protection: Sludge screening in wastewater treatment.
Conclusion
The core reasons for choosing a vibrating screen are its efficiency, flexibility, and reliability. Whether for solid particle classification, solid-liquid separation, or high-precision screening, vibrating screens can meet requirements by adjusting parameters (amplitude, frequency, screen mesh) while balancing cost and maintenance convenience. For most medium-to-coarse particle screening applications, vibrating screens are typically the most cost-effective solution.
Contact Us Today for a Tailored Solution!
Julie
Email: sales@filtrationchina.com
Mobile / WA / WeChat / Line / Viber: +86 159 2865 0174
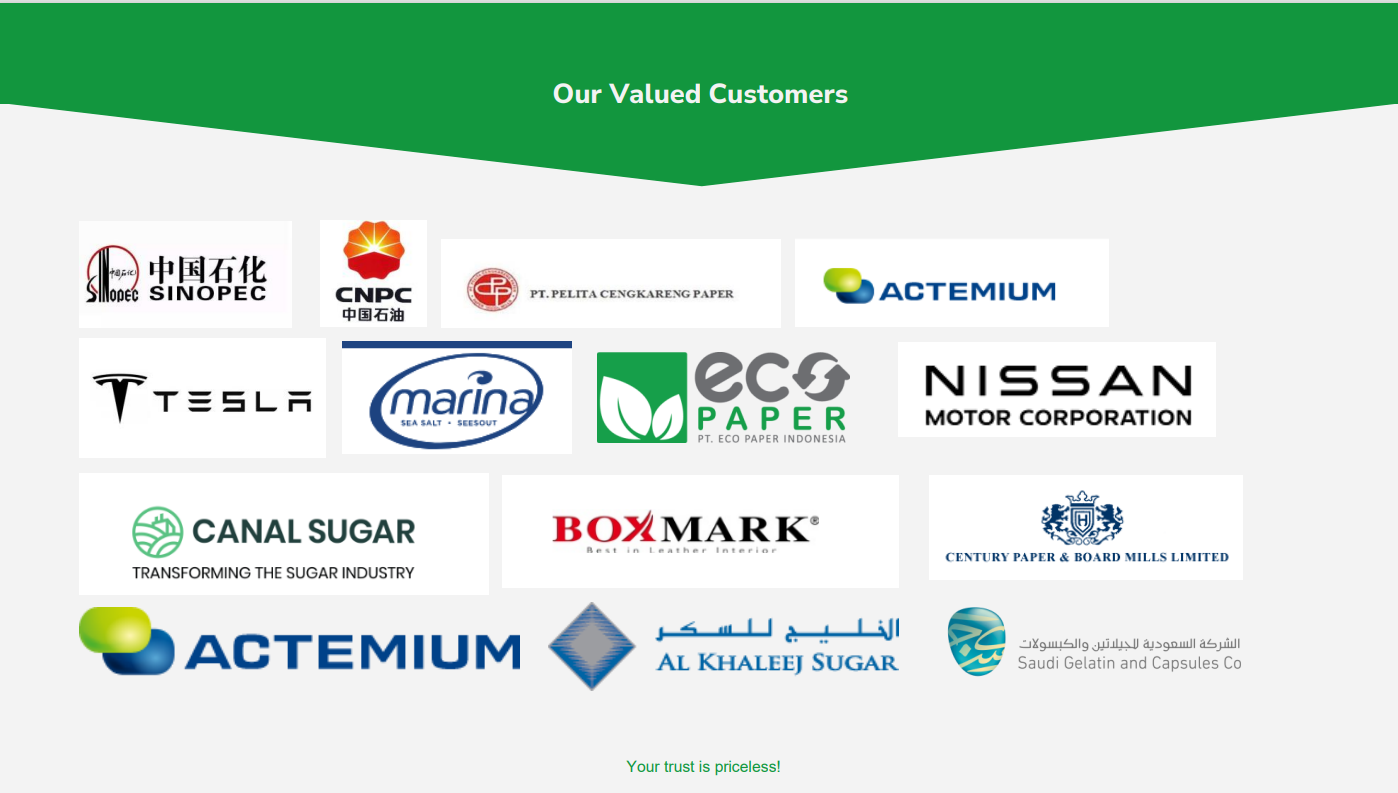