What is a screw press? What is the difference between it and frame, belt, and centrifugal dehydrators?
A screw press is a type of equipment used for sludge dewatering, distinguishing itself from plate-and-frame, belt, and centrifugal dehydrators.
In a screw press, as the screw-driving shaft rotates, multiple fixed and movable discs placed around the shaft move relative to each other. Under the influence of gravity, water filters out through the gaps between the movable discs, achieving rapid concentration. The dewatered sludge moves continuously with the rotation of the screw shaft. Along the mud cake outlet direction, the screw pitch of the screw shaft gradually decreases, and the gaps between the discs also shrink. The volume of the screw chamber continuously contracts. Under the influence of the back pressure plate at the outlet, internal pressure gradually increases. With the continuous rotation of the screw-driving shaft, water in the sludge is squeezed out, and the solid content of the filter cake keeps rising. This process ultimately achieves continuous sludge dewatering. The stacking screw dehydrator integrates the concentration and pressure filtration dehydration of sludge in one cylinder, replacing traditional filter cloth and centrifugal filtration methods.
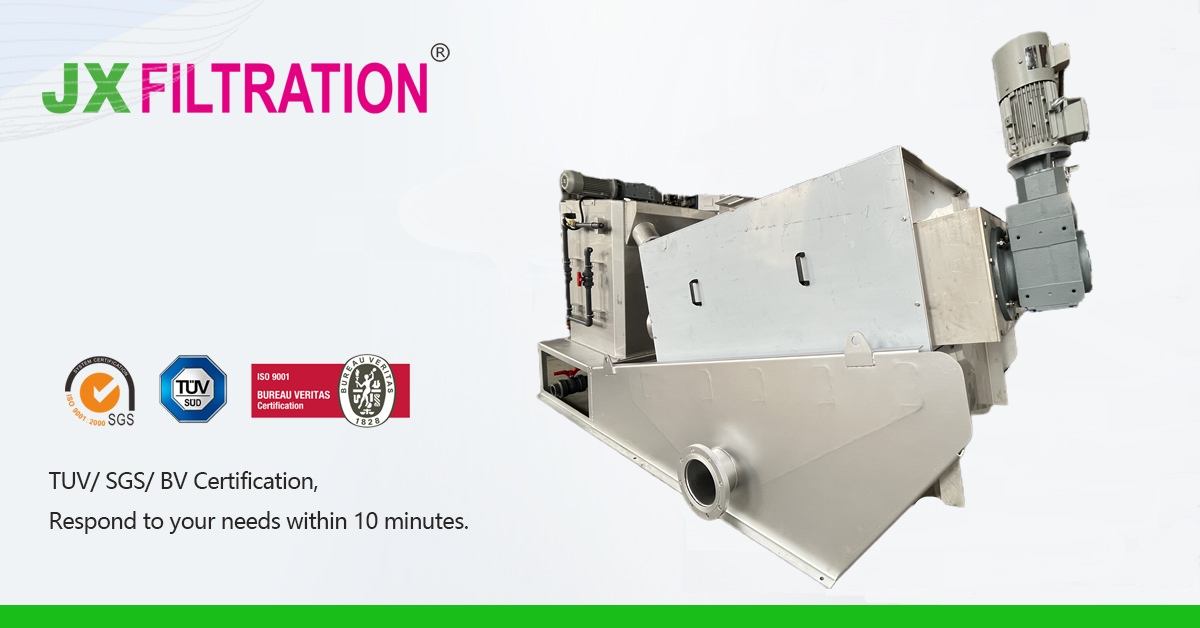
A plate-and-frame filter press achieves dewatering by squeezing sludge through filter cloths with the pressure of plate frames. It is suitable for filtering suspensions with solid particle sizes above 5μm and solid concentrations ranging from 0.1% to 60%. Plate-and-frame filter presses have advantages such as strong adaptability to inlet sludge concentration, high cake solid content, and minimal coagulant dosage (even none in some cases). However, this equipment has a large footprint, operates intermittently, lacks continuous mud inlet processing, and has a lower efficiency. Additionally, the open operation during work results in a poor working environment. Despite these drawbacks, recent developments have allowed plate-and-frame filter presses to meet the requirements of modern sewage treatment plants. Through PLC system control, they can achieve fully automatic operation, significantly reducing labor intensity.
A belt filter press uses two tightly stretched filter belts to carry a layer of sludge. The sludge passes through a series of regularly arranged rollers in an S-shape, relying on the tension of the filter belts to exert pressure and shear force on the sludge layer. This process squeezes out capillary water, resulting in a high-solid-content cake. Belt filter presses have advantages such as low noise, low electricity consumption, and a relatively unaffected sludge outlet effect by inlet load. They are characterized by low cake moisture content, simple management and control, and low requirements for the operator's qualifications. However, they occupy a large area, require a significant amount of flushing water, and are prone to issues like filter belt clogging and belt deviation.
Centrifugal dehydrators consist of a drum and a screw conveyor with a hollow shaft. This equipment has a compact layout, a small footprint, and can significantly reduce infrastructure investment. Centrifugal dehydrators integrate sludge concentration and dewatering into one process, allowing for continuous dewatering with minimal susceptibility to changes in sludge concentration. They produce sludge with a high solid content and a large sludge outlet. Compared to belt and plate-and-frame filter presses, they consume less coagulant and cleaning water, resulting in lower operational costs. However, they have higher electricity consumption and generate significant noise. The outer edge of the centrifuge drum or screw is susceptible to wear. Newer centrifugal dehydrators often have replaceable assembly blocks for the outer edge, typically made of tungsten carbide, but they can be expensive.
A screw press has a small footprint, low water consumption for flushing, low noise, and a good workshop environment. However, individual units have a smaller processing capacity, and the clarified liquid after dewatering has a high solid content. They are primarily used for direct dewatering of activated sludge in small sewage stations. In sewage station construction, the design of sludge concentration tanks can be omitted, saving costs. When processing the same amount of sludge, screw press can save 85% of energy compared to centrifugal dehydrators, and their footprint is only half as much. In terms of surface cleaning, screw press can save 95% of water compared to belt filter presses. Screw press are particularly suitable for handling oily sludge, such as fiber residues from food processing plants subjected to pressurization. The moisture content requirement for stacked screw dehydration is generally 95% to 99.5%, with an outlet sludge moisture content typically ranging from 75% to 80%.
Any Requirements, Contact Us Now!
Nina
Email/Teams:nina@filtrationchina.com
Mobile/Whatsapp/Wechat: +86 17269571060
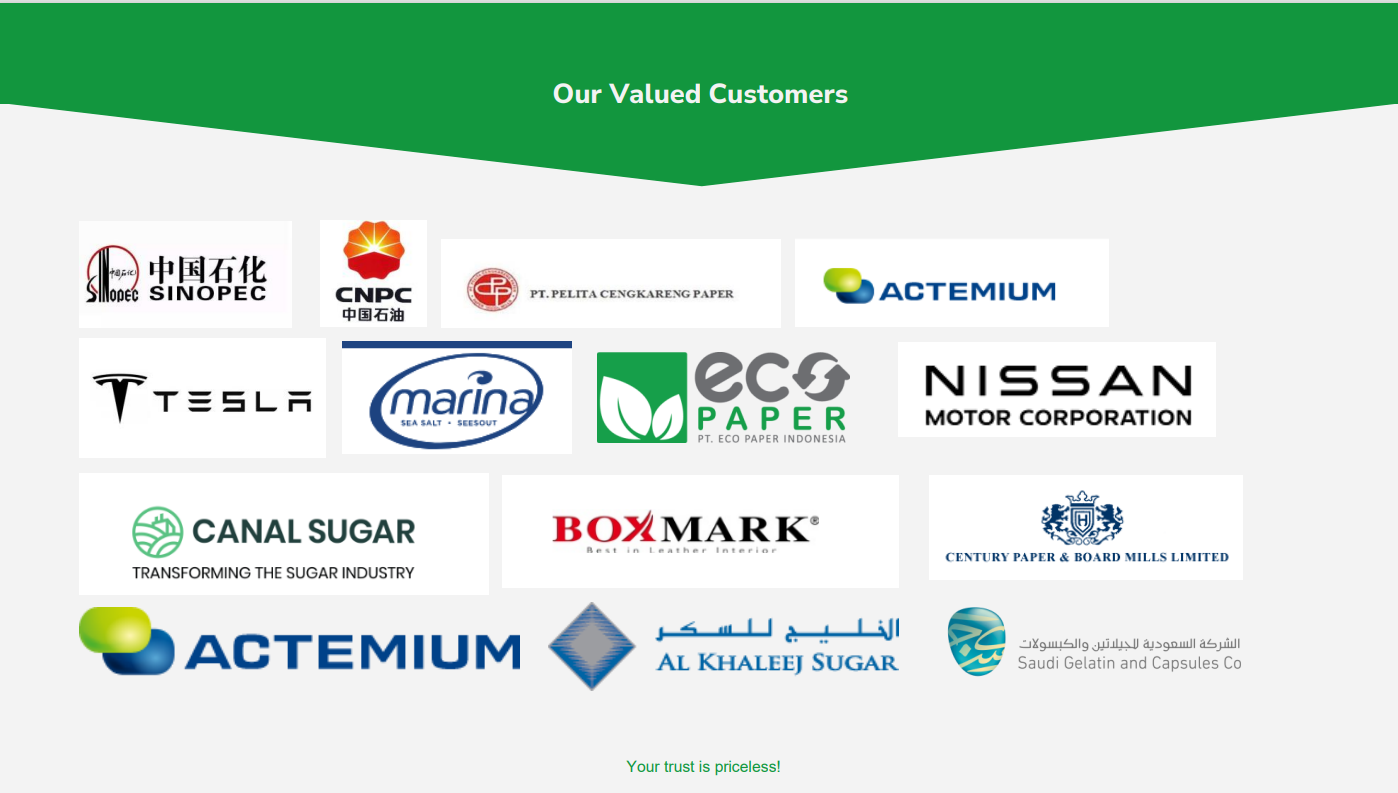